Solarkraft ernten
Hoch- und Tiefpunkte
Unweit von Las Vegas werden wir Zeugen einer neuen Schöpfungsgeschichte: Eine innovative Technologie bereitet den Boden für die andere. Genau dort werden über 300 Acres (120 Hektar) Buschvegetation in der Wüste in eine der modernsten Solarfarmen im Südwesten der USA umgewandelt.
Sobald die Anlage fertiggestellt und am Netz ist, kann sie 30 Megawatt Strom erzeugen – genug, um 2.500 Haushalte ein Jahr lang zu versorgen. Ein enger Terminplan und große Mengen zu bewegender Erde erhöhen ebenso wie die steilen Abhänge und Geländeverschiebungen den Schwierigkeitsgrad der Umsetzung – eine Herausforderung, die durch den Einsatz von Satellitenortung und einer kleinen Flotte GNSS-gesteuerter Grader gelöst wird.
Den Managern von Aggregate Industries, einem Subunternehmen, war klar, dass mit herkömmlichen Vermessungs-, Planungs- und Erdbewegungsverfahren das Projekt beinahe ein Ding der Unmöglichkeit sein würde. Aber so heißt es bei den erzielten Fortschritten: Es werde Licht (oder zumindest Strom).
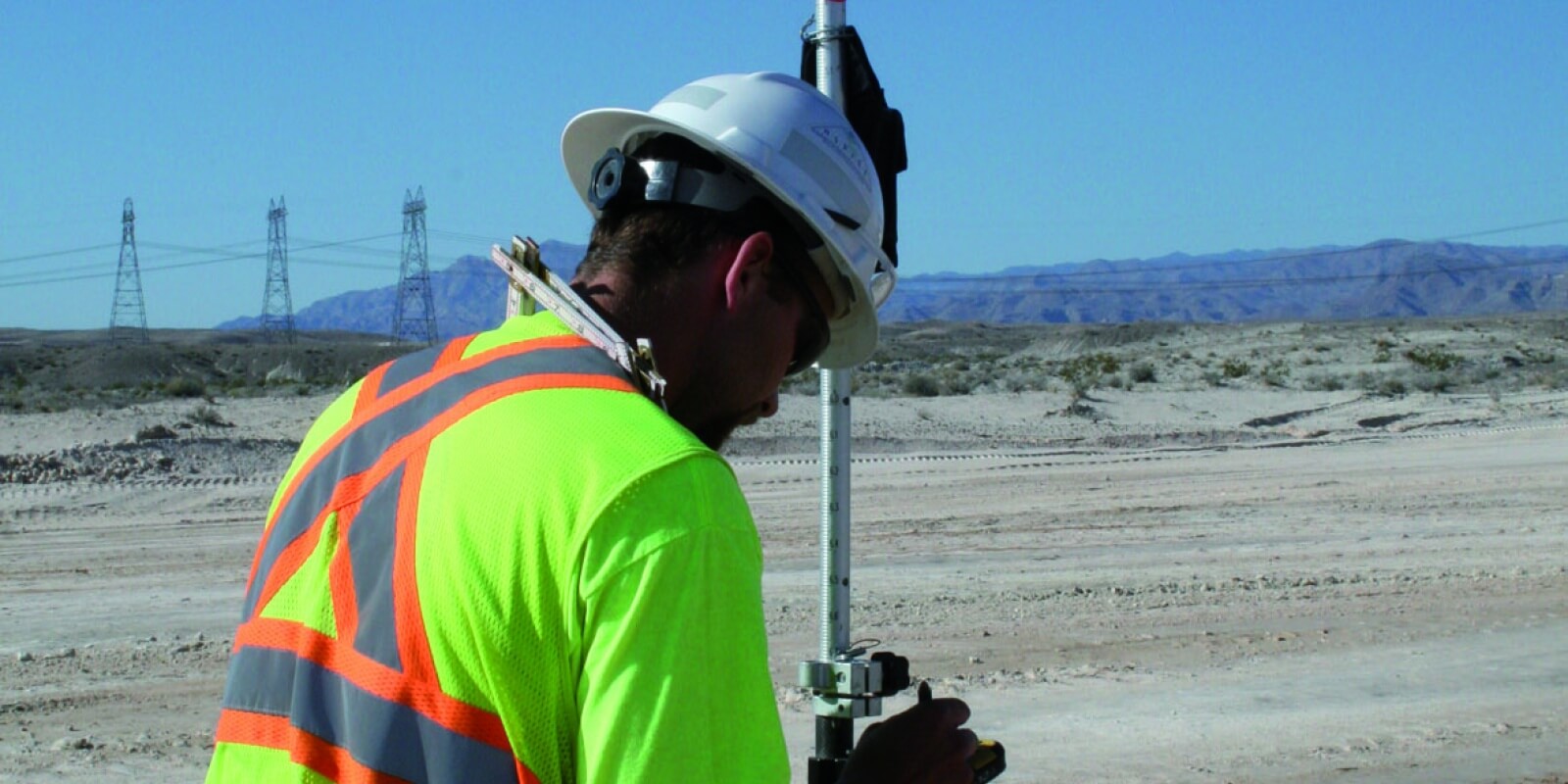
Wir wussten, dass das hier kein normaler Planierjob sein würde!
Effizienz in ihren Händen
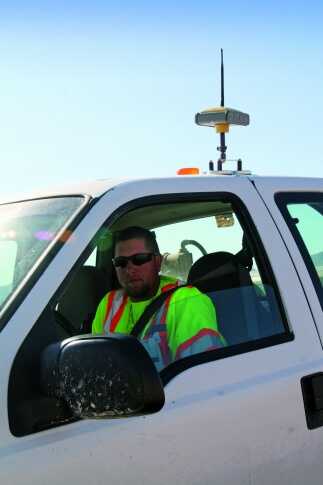
Das Projekt Spectrum Nevada Solar Farm ist nicht einfach nur ein Großprojekt, sondern auch eines der effizientesten im Staat Nevada. Die komplette Anlage besteht aus 130.000 PV-Solarmodulen und 2.000 Trackerreihen, die in der Lage sind, die Stromerzeugung der Solarfarm um über 20 Prozent zu steigern. Bauführer Ryan Baxter zufolge nahm Aggregate Industries im Dezember 2012 die Arbeiten auf, die jetzt soweit fortgeschritten sind, dass die Anlage bereits Strom erzeugt.
„Am Anfang haben wir eine riesige Fläche mit Wüsten- und Buschvegetation gerodet, ein Rückhaltebecken und einen Lagerbereich angelegt, dann ging es weiter mit der Aufstellung. Wir wussten, dass das hier kein normaler Planierjob sein würde. Der nivellierte Teil verwandelte das Gelände in ein Modell nach ausgeklügeltem Konzept: Auf jede höher gelegene Linie folgt eine niedrige Ablauflinie, die dann wieder bis zu einem hohen Punkt ansteigt. Dies wiederholte sich, damit etwaiges Wasser „vom Gelände in die tiefer gelegenen Bereiche abseits des Projektareals ablaufen würde.“
Aggregate Industries hat seinen Bestand an GNSS-Ausrüstungen über den Topcon-Händler Nevada Transit & Laser um 3D-MC-Maschinensteuerungen von Topcon für drei seiner Grader CAT 14H erweitert.
Die feinen, einen halben Meter hohen Wellen im Boden, die Baxter meint, wiederholen sich alle 20 Meter, sodass 38 Reihen mit hohen und tiefen Punkten entstanden sind. Diese Züge mittels „herkömmlicher Vermessungs- und Planierverfahren zu gestalten, wäre ein Albtraum gewesen“, meint er. „Dank der Topcon-Steuerung gelang das Abstecken der Polylinien am Abhang leicht und schnell.“
Bei den anderen Solarfarmprojekten, an denen Aggregate Industries beteiligt war, fiel nur geringer Abtrag an. Durch die bei diesem Projekt erforderlichen Wellen gab es Bereiche mit Ab- und Auftrag in einer Größenordnung von 30 Zentimetern bis zu 2,5 Metern.
„Man kann den Einfluss, den tragbare Steuerungen auf den Betrieb haben, gar nicht genug hervorheben“, führt er aus. „Dass wir alles jederzeit in der Hand hatten, hat einen gewaltigen Unterschied ausgemacht. Bei diesem Teil konnten wir die Fertigstellungszeit leicht um die Hälfte reduzieren.“
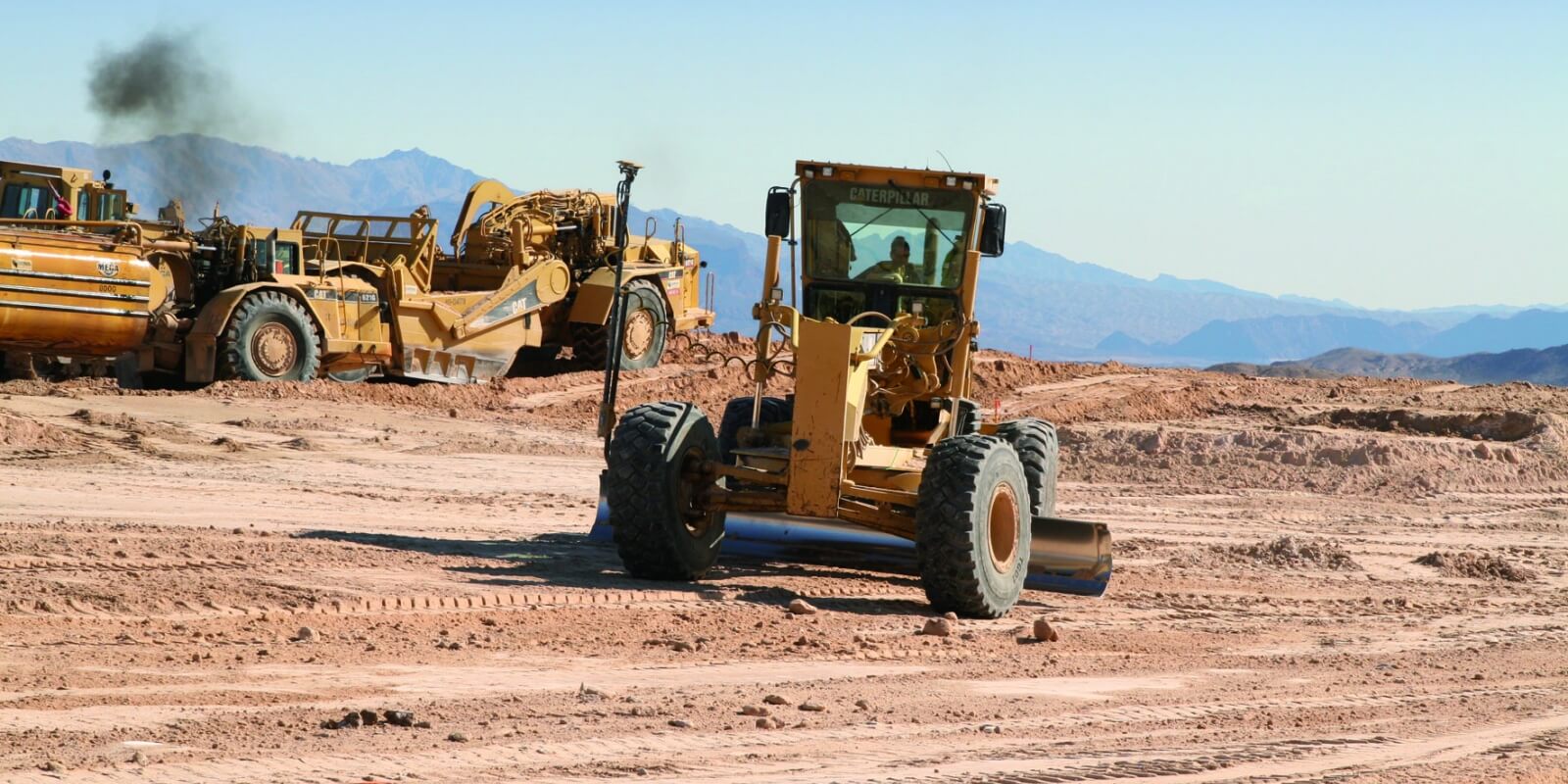
„Durch diese drei Schilde gelang auch die Feinnivellierung schnell und leicht – insbesondere angesichts der vielen Neigungswechsel hier.
Früh zur Messe
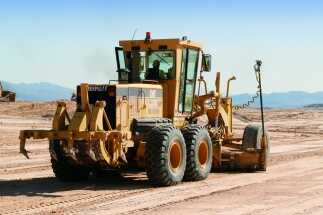
Ein ganze Armada an Planierraupen, Bodenverdichtern und Schürfladern übernahm die Schwerstarbeit bei diesem Projekt: Sie bewegten über 550.000 Kubikmeter Schutt und Steine. Den Rest der Planierarbeiten übernahm ein Trio aus maschinengesteuerten Gradern. „Durch diese drei Schilde gelang auch die Feinnivellierung schnell und leicht – insbesondere angesichts der vielen Neigungswechsel hier“, so Baxter. „Dass jeder Bediener seine Position im Gelände jederzeit auf dem Kabinenmonitor sehen konnte, hat auch viel ausgemacht.“
Wenn bestimmte Werte bestätigt werden mussten – zum Beispiel die Menge der innerhalb eines bestimmten Zeitrahmens bewegten Erde – lieferte GNSS zuverlässige Zahlen. „Mit einem GNSS-Rover kann man das Gelände abgehen, topografisch erfassen und als Geländemodell speichern. Nach dem Abtragen und Auffüllen erstellte ich einfach ein neues Geländemodell und verglich die beiden. Dadurch wusste ich ganz genau, wie viele Meter wir zusätzlich bewegt hatten. Das ist bei jedem Job ein enormer Vorteil.“
Prüfung im Pickup
Als Bauführer leitet Baxter die Qualitätskontrolle bei den Projekten von Aggregate Industries – normalerweise ist das eine leichte Aufgabe. Allerdings sieht das bei einer Solarfarm solch riesiger Ausmaße ganz anders aus. Mit einer Nivellierlatte in der Hand die Höhen auf einem Gelände mit diesen Ausmaßen und solcher Komplexität zu prüfen, kann schon entmutigen und ist, was noch wichtiger ist, sehr zeitaufwendig. Also befestigte Baxter einen GNSS-Empfänger auf dem Dach seines Pickups, fuhr über das Gelände, prüfte die Höhen und nahm bei Bedarf Korrekturen vor.
„Eine tolle Lösung“, sagt er dazu. „Wenn man den Rover vom Stab abnimmt und oben auf dem Auto befestigt, dann ist der Höhenunterschied nur minimal. Also habe ich mir den Feldrechner geschnappt und bin damit das Gelände zur Prüfung abgefahren. Genau das Gleiche, als ob ich das Gelände zu Fuß abgehen würde – nur viel schneller. Ich konnte über ein Gebiet fahren, das gerade bearbeitet wurde, und wusste genau, wie es läuft. Dadurch verlief die Fertigstellung immer auf hohem Niveau. Und die Technologie wird uns auch bei zukünftigen Projekten von Vorteil sein.“