BIM Gets a Boost
High-speed precision scanning technology brings cost-effective precision to structural steelwork at Nashville’s Music City Center
The 1.2 million-square-foot Music City Center in Nashville has 11,000 tons of structural steel, including the interior backbone of what is arguably the facility’s most distinctive architectural feature: a 162-foot wall at the north end of the main structure that rises out of the main roof and resembles the body of a guitar from a bird’s-eye view. This ‘backbone’ was erected by one of the steel contractors on the project, Schuff Steel Atlantic.
Laying out the structural steel for the radial shape of the guitar wall for the facility, which opened in 2013, presented Schuff with a significant challenge. The contractor used high-speed precision scanning technology, a key tool in Building Information Management (BIM), to meet it.
Staying in tolerance
The design tolerances were one-quarter of an inch and three-eighths of an inch around glass. Schuff Project Superintendent John Fugera noted that a failure by Schuff to adhere to the tolerances would force work from contractors installing glass, cut stone and metal panels out of tolerance, too.
In March 2011, Schuff began laying out and erecting the steel framework for a straight section of the guitar wall on the north side of the building using a total station. When Schuff got to the curved section, it opted for its first-ever use of laser scanning—in this case, GLS-1000 and GLS-1500 laser scanners rented from Earl Dudley, Inc., a surveying and geospatial equipment dealer with locations in the Southern United States.
The GLS-1500 collects points at a rate of 30,000 points per second and a range of 150 meters. Topcon Precise Scan technology is designed to allow high-accuracy measurements over a wide range of distances. Lens array optics technology maintains distance accuracy from 1–150 meters and additional ranging past 330 meters is possible.
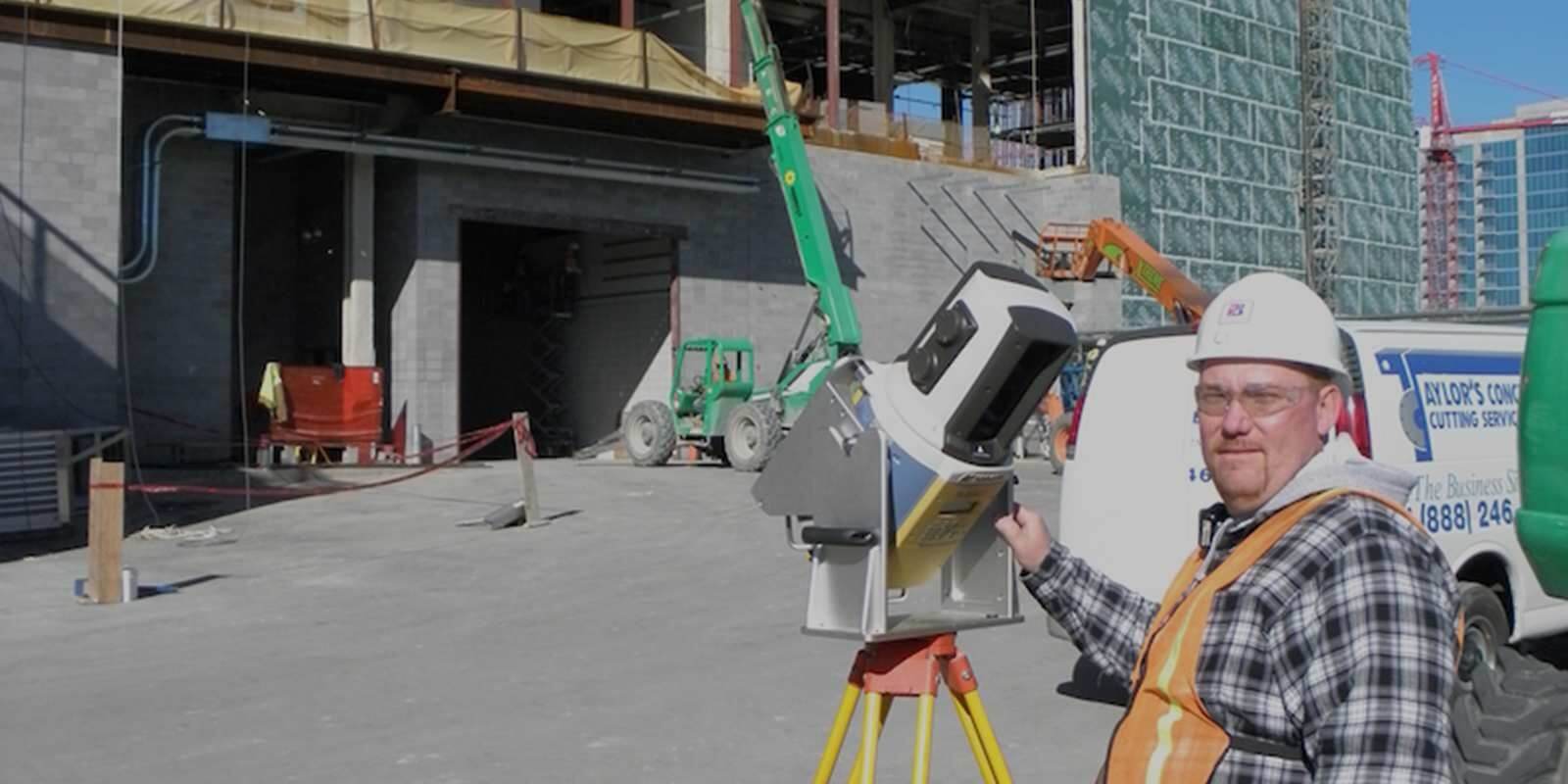
"The point cloud and the scan give me the whole face of the building and let me know exactly where everything is."
Scanning aids efficiency
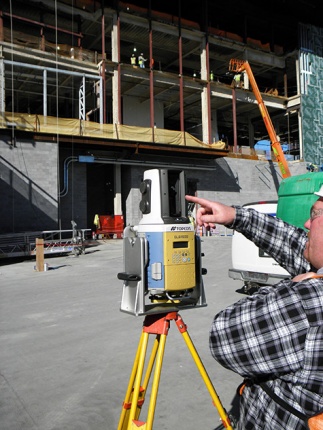
Ensuring adherence to design tolerances would have been especially cumbersome on the east side of the Music City Center, where the guitar wall on this side featured eight radius variations and five pitch variations at the roof. Fugera estimated that it would take at least two weeks to shoot the estimated 2 million points required to as-built survey Schuff’s steelwork on the long east side of the guitar wall and three or four more weeks to determine where Schuff’s steelwork was located relative to the main steel structure. The laser scanner also allowed surveying from ground level, whereas the total station would have been operated on an aerial lift at various levels.
In late fall 2011, Chris Clay, RLS, Schuff’s licensed surveyor on the project, set up the scanner outside of the guitar wall at ground level near the southeast corner of the facility. He identified several magnetic targets that had been placed on several steel beams forming a large horizontal rectangle on the eighth level. The target locations were surveyed with a total station and tied to the grid formed by control points based on the official building survey and a three-dimensional BIM model of the entire building. He measured the center of the targets from building control points using a total station and scanned the targets. The scanner resectioned in order to establish the position of the instrument relative to each target. By doing this, Clay tied the target locations to both the building model and the official survey grid.
He tilted the scanner at a 45-degree upward angle and entered the project number into the GLS-1500 keypad. Clay scanned the targets from left to right and then bottom to top. Raw point cloud data were copied from the data card in the scanner and sent to Adam Arrington, PE, at Earl Dudley, who imported them into Topcon ScanMaster software. He registered the data together in ScanMaster, essentially performing quality assurance/quality control on the data, and stripped the file down into Schuff’s steelwork and surrounding structures that Fugera needed to view in order to ensure correct relative positioning.
Taking a PCG file provided by Arrington, Fugera imported the point cloud and dimensional data into AutoCAD using kubit software. The kubit software allowed Fugera to compare the point cloud coordinates with the AutoCAD building model that is based on the official survey. ScanMaster Viewer allowed him to view images of Schuff’s steelwork from where the scanner was located and point coordinates. Along with the ScanMaster and AutoCAD files, Fugera viewed Schuff’s steelwork against the entire building structure on a structures file developed by Schuff’s drafting department.
“The point cloud and the scan give me the whole face of the building and let me know exactly where everything is,” Fugera said.